What is CAD (Computer Aided Design)? Definition, Types, and Applications
Computer-aided design (CAD) allows humans to digitally create two- and three-dimensional design simulations of real-world objects. This allows for the adjustment and modification of designs before using any resources to physically create the object.
Before computers became commonplace, designers used slide rules, drafting triangles, and large sheets of paper to create technical drawings by hand. Computer-aided design (CAD) has made the process faster, less expensive, and more efficient.
In this article:
What Is CAD (Computer-Aided Design)
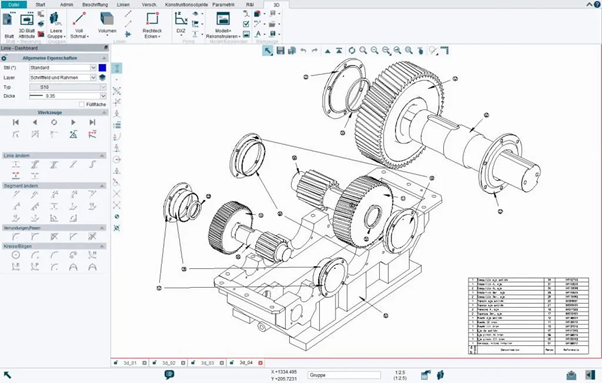
Example of a CAD drawing
CAD is also sometimes called “computer-aided design and drafting” (CADD). Using computer-based software to assist in design processes is known as computer-aided design. Various kinds of engineers and designers regularly utilize CAD software. Two-dimensional (2-D) drawings and three-dimensional (3-D) models can both be produced using CAD software.
By making designs simple to share, review, simulate, and edit using 3D CAD, you can quickly bring new, unique items to market. When it comes to the conventional “pencil on paper” method of engineering and design, known as manual drafting, CAD software has supplanted the T-squares and protractors employed in the past.
PRONTO, created by Dr. Patrick J. Hanratty in 1957, was the first commercial numerical-control programming system and earned him the moniker “Father of CAD/CAM.” SKETCHPAD, developed by Ivan Sutherland in 1960 at MIT’s Lincoln Laboratory, made things user friendly by introducing the first graphical user interface and by allowing users to designate a “master” drawing that could be used as a base for multiple “occurrences.” The program proved the viability and fundamentals of computer-aided technical sketching.
When CAD was first developed, these programs ran on university computers that had minimal computing power which, prevented them from being a viable business option. It wasn’t until the mid 1960s that IBM’s Drafting System made computer-aided design systems more accessible and affordable for companies. Today, engineers employ CAD files that accurately depict an object’s attributes in both 2D and 3D models.
How does computer-aided design work?
A standard CAD system requires the installation of a CAD software package and, typically, a graphics card. The graphics kernel acts as the brains of a CAD software application. The graphical user interface (GUI) displays the CAD geometry, collects user input, and is a crucial component of CAD software.
CAD models often provide a three-dimensional representation of a component or a whole system on a computer screen. The user controls the characteristics and relationships that comprise the model, including geometry, shape, and size. Developers can easily modify the model by altering parameters, which makes it easier to conceptualize how changes might impact the final design.
The GUI transfers data from input devices, like a mouse, keyboard, or trackball, to the graphics kernel in an appropriate format. The graphics kernel then creates the geometric entities and instructs the graphics card to show them on the user’s screen.
Design engineers may plan and create their work on a computer screen with CAD, print it, and save it for upcoming revisions.
CAD software represents the objects of traditional drafting using either vector-based visuals or, in some cases, raster graphics to show the overall appearance of planned things. However, it goes beyond representing simple forms.
Individual CAD programs may output different data with the design, including required materials, procedures, measurements, and tolerances, just as a hand-drawn technical or engineering drawing may include annotated information. The software also documents how various materials and stakeholders interact, emphasizing the task’s importance as stakeholders add more details to the drawings throughout the product lifecycle.
Types of CAD
Computer-aided design (CAD) consists of two broad types – 2D and 3D. However, you can further categorize them into the following:
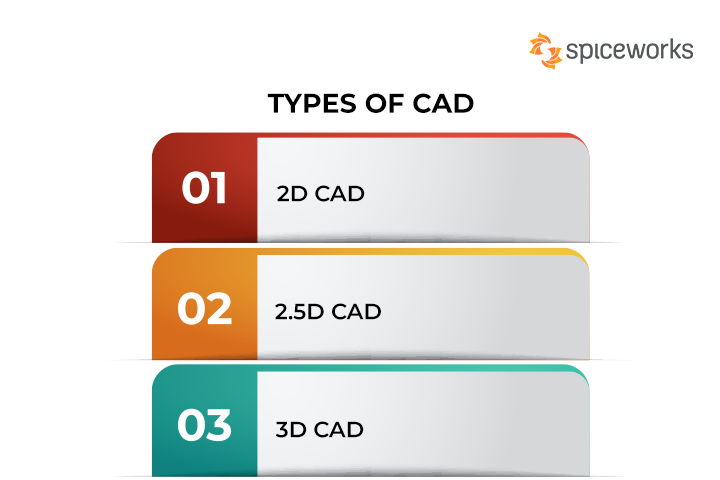
Types of CAD
1. 2D CAD
Early in the 1970s, 2D CAD, the industry’s first CAD system, was created. At that time, large aerospace, automotive, and other engineering businesses developed internal technologies to automate repetitive drafting tasks.
2D CAD uses fundamental geometric shapes like lines, rectangles, arcs, and circles to make flat drawings. 2D CAD software also annotates drawings using text, dimensions, leaders, and tables. This type of CAD is used to design, plan, section, and detail structures and represent elevation views in the built environment. Additionally, the drawings convey how various components work together to form assemblies and offer insight into potential locations that may require additional inspection.
A library of geometric images, the capacity to design Bezier curves, splines, and polylines, the ability to specify hatching patterns, and the ability to generate a bill of materials are all standard features of 2D CAD systems. AutoCAD, KeyCreator, CATIA, and MEDUSA4 are well-known 2D CAD applications.
2. 2.5D CAD
2.5D CAD is an intermediary design tool that combines 2D and 3D CAD aspects. It represents the depth of objects in geometric shapes similar to 2D CAD, but it also uses contour maps to visualize the object’s height at various points. It is primarily used in computer numerical control (CNC) machining to simplify the creation of parts with multiple flat surfaces at varying depths
3. 3D CAD
3D CAD has grown in popularity as a design tool as computer processing power and graphic display capabilities have improved. In general, 3D CAD software produces a realistic model of an object, enabling designers to address potential issues earlier in the product lifecycle. Like most software, CAD tools may be better for different modeling applications. The three main categories of CAD software modeling are:
- Solid Modeling: A solid model is a 3D image that represents the volume of an object and provides a complete and accurate representation of its geometry.
- Wireframe Modeling: A wireframe model uses lines and curves to represent the edges of an object – essentially, a skeletal view without surface details.
- Surface Modeling: A surface model represents complex surfaces by defining the exterior shape of an object. Designers frequently use this model type for intricate and detailed designs.
Notable 3D CAD applications include Inventor by Autodesk, ZW3D, Blender, and CATIA V5.
CAD File Formats
CAD software stores in one of two file formats: “native” or “neutral.”
1. Neutral file formats
Neutral file formats are designed to be used across various different software systems. They are designed to be more universal so that users can work amongst several software packages. The STEP format (STandard for the Exchange of Product model data) is commonly used to deliver the necessary information regardless of the software tool being used. Neutral file types include STEP (.stp, .step); Stereo Lithography, or STL (.stl); Initial Graphics Exchange Specification, or IGES (.igs,.iges); 3D Portable Document Format, or PDF (.pdf); Drawing Interchange Format, or DXF files (.dxf), although numerous types exist. CAD-neutral file formats improve interoperability, but they do not all behave in the same way, carry the same data, or import or export as expected.
2. Native file formats
Some CAD software tools exclusively use specific file formats, or native CAD files. These file types are typically only viewable with the same program that created them. Attempting to use them with any other software may not work as intended. Using native CAD files is the best way to ensure to the best possible performance of the file, as the software will understand how to interpret the data for use with the tool’s functions and features. Native file formats include AutoCAD (.dwg); SolidWorks (.sldprt and .sldasm); CATIA V5 (.CATPart and .CATProduct); and Altium (.SchDoc and *.PcbDoc).
Popular CAD software tools
Designers, engineers, and architects in a multitude of industries use CAD software tools to develop 2D and 3D models. The software assists them in exploring design concepts, visualizing ideas through photorealistic renderings, planning construction or engineering projects, and simulating how a design might function in real life. Designers use some CAD software, like Altium, for niche industry applications, while they utilize other programs, such as AutoCAD and CATIA, across various industries.
-
AutoCAD
AutoCAD, a product of Autodesk, is one of the oldest and most well-known CAD software tools. It has a strong user base in architectural and industrial engineering fields. This CAD program is used for 2D and 3D drafting and design. It can produce designs, equipment layouts, section planes, model documentation, and more. Students, architects, designers, engineers, project managers, surveyors, construction managers, and more use AutoCAD. Pricing starts at $2,030 per year.*
-
SOLIDWORKS
SOLIDWORKS by Dassault Systèmes is built for those who work primarily with 3D designs. While it is capable of 2D modeling, it is a feature-based, parametric model. This 3D modeling CAD software is widely utilized in the mechanical engineering fields, and boasts that it is “built by engineers, for engineers.” Pricing starts at $2,820 per year.*
-
CATIA
Also built by Dassault Systèmes, CATIA is a more advanced tool used for computer-aided design, manufacturing, and engineering. It is sometimes referred to as a 3D product lifecycle management tool. It is popular within the aerospace and defense industries, and is used by organizations including Boeing, NASA, VW, and Lockheed Martin. Pricing starts at $7,560 per year, plus a quarterly subscription fee of $2,268.
-
Altium
Altium is purpose-built for designing printed circuit boards (PCBs), which are standard elements in most electronic devices. It assists designers in managing complex circuitry, including high density interconnect (HDI) boards. Designers can create electronic designs that span the lifespan of the board – from schematics all the way to manufacturing files. Pricing starts at $4,235 per year; or companies may choose a perpetual license starting at $11,970.*
-
FreeCAD
FreeCAD is an open-source 3D modeler that can create 2D and 3D drawings, and can be used for a multitude of use cases, including product design, mechanical engineering, and architecture. The advanced geometry engine is based on Open CASCADE Technology. The tool supports multiple use cases, includeing 2D CAD drafting, architectural modeling, CNC design, and more. It is free to download and use and available for Windows, Mac, and Linux.
*Note: Prices based on information available on vendor websites and are accurate as of September 2024.
Common Applications of CAD
Since CAD aids in numerical data modeling, simulation, and design, its applications cut across industries. Some of its critical use cases include:
1. Aerospace and Transportation
Vehicles like cars, trucks, airplanes, and space shuttles are often initially prototyped using a CAD tool. Once designed, the models can be tested for aerodynamics, structural integrity, and safety before physical construction begins. Additionally, the CAD data is used in automated manufacturing processes to ensure consistency and quality.
2. Architecture
Blueprints are technical drawings that denote any layout, like a floor plan, elevation, or section. Floor plans and scaled diagrams depict the size, location, and shape of rooms and other objects within a structure and are shown from the top down. CAD simplifies the production of these 2D and 3D representations. Architects can use their models to simulate structural integrity, energy efficiency, and lighting before construction begins.
3. Civil Engineering and Public Services
Civil engineers work with utilities and other infrastructure like roads, bridges, water systems, waste disposal, and more. CAD allows these engineers to create detailed representations of infrastructure, including topographic, cadastral, and navigational maps. Civil engineers use CAD models for maintenance projects and to assist in simulating how changes to the landscape may impact existing resources.
4. Engineering and Construction
CAD tools streamline the Building Information Modeling (BIM) process, including creating and managing buildings and infrastructure’s digital representation. During the design and drafting phase, engineers use 2D and 3D drawings. Models also simulate the building’s structural integrity during different physical conditions. CAD also makes it easier for other architects, engineers, and contractors to collaborate during various project phases.
5. Life Sciences and Healthcare
The medical industry benefits from CAD in many ways. This allows manufacturers to uniquely design and create prosthetics, implants, and other medical devices for individual patients.
6. Product Design and Manufacturing
As in other industries, CAD software allows product designers and manufacturers to create 3D models of products before investing in physical prototypes. These models can simulate real-world conditions to predict the product’s durability, performance, and functionality. CNC machines use tool paths built on CAD models. Drawings for additive manufacturing applications also use CAD files in the creation and preparation stages. Additive manufacturing, also known as 3D printing, uses an additive technique that involves building up successive layers of material.
Takeaway
Computer-aided design (CAD) is a crucial field in product engineering and the industrial sector. It allows engineers to develop, test, and optimize their design in a safe environment, without having to build expensive prototypes. CAD software also provides a documentation trail, records specifications, and enables collaboration between multiple disciplines and stakeholders in product manufacturing. That is why organizations need to understand how computer-aided design works and its key concepts.